In addition to the injection vowin.cn/en/News/news1251.html' target='_blank'>vowin.cn/' target='_blank'>molding machine, the process of injection molding requires not only the engineer to effectively control each plastic injection molding processing, but also the injection molding engineer to be able to master the use of the injection mold.
As one of the important components of injection mold, the types of plastic injection molding gate are diversified, and different types of injection molding gates are used in different molded plastic parts, and they also have an impact on the final quality of injection molding project parts.
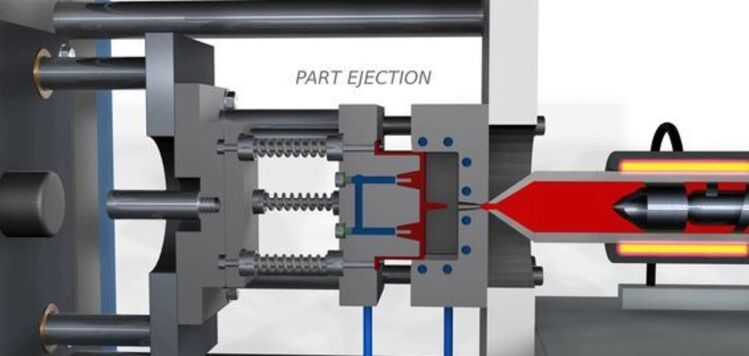
What is an injection molding gate?
The gate can be understood as the last “door” for the molten plastic material to enter the cavity through the pouring system, and is the feeding channel connecting the manifold and the cavity.
The gate is also called the feeding, it is the narrow opening between the manifold and the cavity, and it is also the shortest part.
What is the role of the injection molding gate?
Its role is to make the molten plastic material acceleration when entering the cavity, which is conducive to filling the cavity quickly, condensing the plastic at the gate after molding to close the cavity and prevent the backflow of molten plastic, avoiding the cavity pressure from falling too fast to produce shrinkage or depression on the product, and facilitating the separation of the casting condensate from the product after molding.
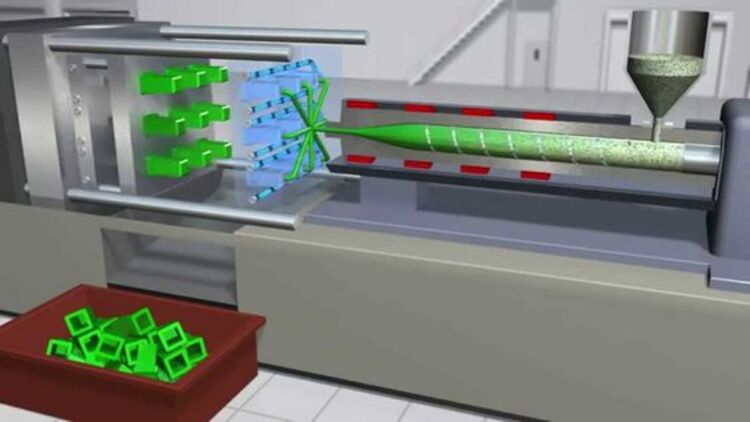
What are the functions of the injection molding gate?
Firstly, it plays a controlling role in plastic flow melt into the cavity.
Second, when the injection pressure is withdrawn, the cavity is blocked so that the plastic in the cavity that has not yet cooled and cured will not flow backwards.
Common types of gates of injection molding parts
Depending on the material, size and surface requirements of the product, the choice of the correct gate placement, the proper gate sizing and the injection gates types will have a critical impact on the quality of the plastic injection molded product.
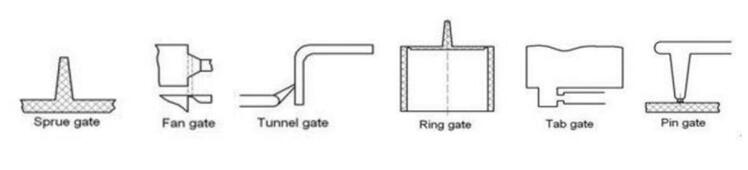
When doing mold design, designing the right way of gate can save the project cost to a great extent. Some products’ gate can be separated from the product automatically trimmed gates, some need to manually trimmed gates, while there are some ways of gate can be trimmed without trimming.
If the number of products is relatively large, you can choose hot runner gate, hot tip gates, valvae gates. This type can save the runner material.
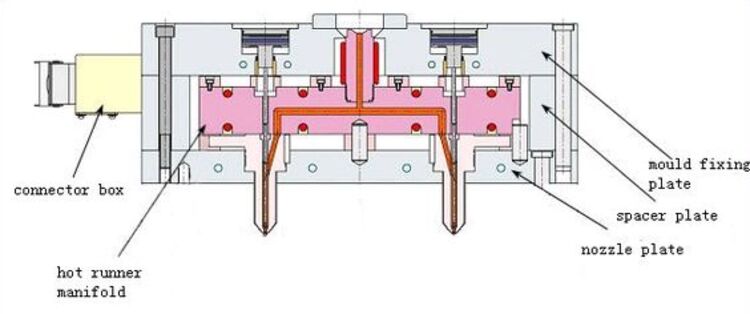
a. Direct gate
The melt enters the cavity directly from the nozzle through the custom injection moulding gate, the process is short, the feeding speed is fast and the molding effect is good. Since the cross section of direct sprue gate is generally larger, the pressure and heat loss are smaller, the pressure retention and shrinkage is strong.
Advantages and disadvantages
Moreover, the mold structure is simple, easy to manufacture and low cost. Its disadvantage is: the cross-sectional area of straight gate is large, so it is difficult to remove the gate, and the traces are obvious after the gate is removed, which affects the beauty of the products.
b. Edge gate
It is also called rectangular gate, tab gate is one of edge gates. It is generally located on the parting line surface and feeds from the outside of the cavity. Since the size of edge gate is generally small, the relationship between cross-sectional shape and pressure and heat loss is negligible.
Advantages and disadvantages
The shape of edge gate is simple, easy to process, easy to accurately control the size and easy to change quickly, suitable for all plastic materials except polycarbonate (PC).
The disadvantage is that the product surface has obvious sprue defects and the sprue needs to be cut manually. It is not suitable for thin and transparent products, and it is also not suitable for thin and long barrel-shaped products.
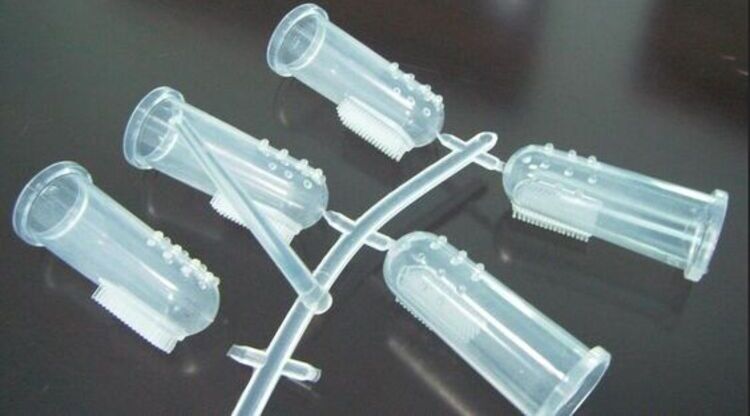
c. Pin gate
Pin gate is also called needle gate. The residual stress near the gate is small and it can pull off the gate by itself, which can realize automatic production. The mold structure is more complicated and the molding cycle is longer.
Generally refers to the small gates less than 1mm in diameter in injection molds. The residual trace on the part is very small and the gate cures quickly and is easy to remove.
However, the material has a tendency to condense in the small hole, and is generally used for small parts and resins with good flowability. Resins with viscosity sensitive to shear are subjected to strong shear when passing through the pin gates, which improves its flowability and thus its mold filling ability.
d. Submarine gates
It is also called submarine gates, tunnel gates, banana gate. The submarine gate can be machined to the exact size and there is no problem with the shape.
When the sub gates is demolded, it can be automatically removed from the product, which is suitable for automated production. However, it is not recommended for PC, PMMA and SAN products.
e. Ear gates
It is also called ear sprue, wing sprue. It is suitable for all plastic products that do not allow the appearance of gate marks on the surface, and can reduce the flow marks produced by the side gate. It is not suitable for PVC and PU plastic products.
f. Fan gates
This type of gate is usually used for injection of thicker parts, which can be injected at a lower speed without solidification. This is suitable for injection molding processes that require low injection stress or warpage and dimensional stability. Gates require taper in both width and thickness to maintain a continuous cross-sectional area.
This ensures.
1. Constant melt speed
2. Consistent flow over the entire width
3. Consistent pressure over the entire width
For other artificially removed gates, the maximum thickness does not exceed 80% of the part thickness. The part width can be varied from 6 mm to 25% of the cavity length.
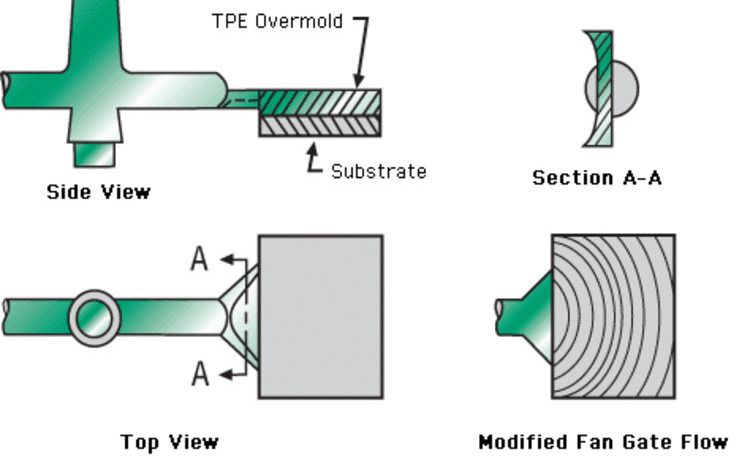
Advantages and disadvantages
a. Advantages of fan gates
1. The melt enters the cavity through a gradually unfolding fan shape, so the melt can be distributed more evenly in the lateral direction, which can reduce the internal stress of the product and reduce the deformation.
2. Because the melt is dispersed into the cavity along the transverse direction, so the flow pattern and orientation effect is greatly reduced.
3. Can reduce the possibility of bringing in air, plus the cavity exhaust good, can avoid gas mixed into the melt.
b. The disadvantages of fan gates
1. Since the sprue gate is very wide, it is more work to remove the gate after molding, which is troublesome and increases the cost.
2. There are long shear marks along the side of the product, which affects the beauty of the product, and it will increase the workload if handled again.
The application of fan gate is often used for molding long, flat and thin products, such as cover, ruler, tray, plate, etc. because of the wide inlet and smooth feeding. For plastics with poor flow, such as PC, PSF, etc., the fan gate is also very suitable.
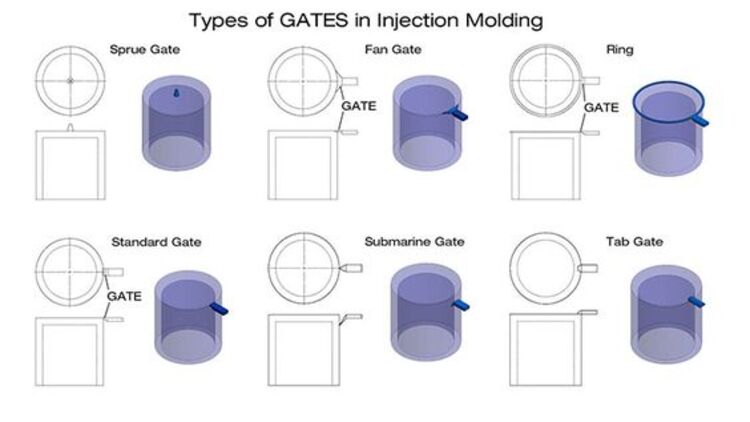
Specification of injection molding gate size
In addition to the injection gate location, the shape and size of the injection molding gate have a great impact on the quality of the part.
The gate is in most cases the part of the runner with the smallest cross-sectional size (except for the injection molding gate of the main flow channel type), and the ratio of its cross-sectional area to that of the manifold is about 0.03-0.09.
The cross-sectional shape is mostly rectangular or circular, and the gate steps are about 1-1.5mm long.
Design principles of the injection molding gate
(1) The gate should be set at the thick wall of the molded product so that the plastic flows from the thick wall to the thin wall to reduce the loss of pressure. The plastic melt should be injected into the cavity quickly with the shortest path and the smallest heat and pressure loss to complete the injection.
(2) The gate should be set at the place where the product can be removed most easily, and try not to affect the appearance (such as possible flow marks).
(3) The location of the gate should be such that when the plastic flows into the cavity, it can flow evenly along the parallel direction of the cavity, and is conducive to the exhaust of the cavity.
(4) The location of the gate should be set to avoid melt marks and flow marks in the important parts of the product, which will reduce the strength of the product.
(5) In case of multiple cavities in one mold, the size and position of the gate should be opened according to the distance between the gate and the main flow channel and the size of the product.
(6) The setting of the gate should avoid the direct impact of the plastic on the weak core, insert, line position, etc. to prevent the deformation of the product.
(7) The setting of the gate should take into account the different shrinkage of the product in the horizontal and vertical directions.
The temperature and pressure of the melt entering the cavity from each gate should be the same to ensure the same shrinkage rate of the products in each cavity.
(8) The turning point of the manifold should be transitioned by arc, and the connection with the gate should be processed into a bevel to facilitate the flow of melt.
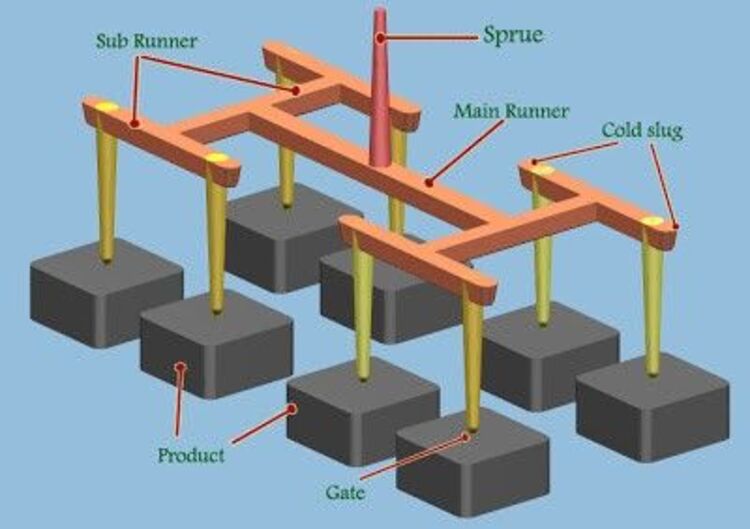
How to choose a reasonable type of gate for different injection molded products?
The choice of gate type depends on factors such as the requirement of product appearance, size and shape constraints and the type of plastic used.
A small gate is generally used because it has the following advantages.
First, small gates can increase the flow rate of the material when it passes through. There is a large pressure difference between the two ends of the small gate, which reduces the apparent viscosity of the molten plastic and makes it easy to fill the mold.
Secondly, the small gate can increase the temperature of molten plastic and increase the fluidity. The friction resistance at the small gate is large, when the molten plastic passes through the gate, part of the energy is transformed into friction heat and heats up, which is good for improving the quality of thin-walled plastic parts or plastic parts with fine patterns.
Thirdly, small gates can control and shorten the time of replenishment, reduce the internal stress of plastic parts and shorten the molding cycle. In the injection, the pressure-holding stage continues until the gate condenses.
The small gate condenses quickly and the replenishment time is short, which reduces the condensation orientation and condensation strain of macromolecules and greatly reduces the internal stress of the replenishment.
The closure of small gates can also correctly control the replenishment time and improve the quality of plastic parts.
Fourth, the small gate can balance the feed rate of each cavity. Only after the flow channel is full and has enough pressure, the cavities can be filled with similar time, which can improve the imbalance of the feeding speed of each cavity.
Fifth, it is easy to trim the plastic parts. Small gates can be quickly removed by hand. Small gates leave small traces after removal, which reduces the trimming time.
However, too small gate will greatly increase the flow resistance and prolong the mold filling time. High viscosity molten plastic and molten plastic with small shear rate effect on apparent viscosity should not be used.
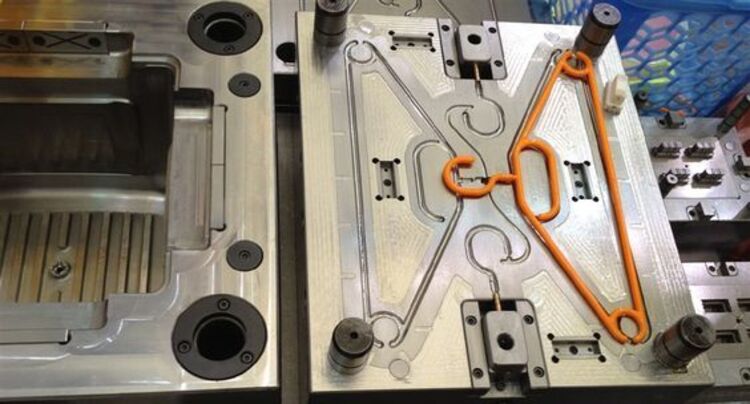
Conclusion
Now you should have some understanding of the type of injection mold gate. If you have a project that you are planning to make an injection mold, find an experienced injection mold supplier and confirm with the mold design engineer before you start to make the mold, such as the location of the injection gate in the DFM and other details to ensure the successful completion of the project with injection moulding supplier.